Dessins ISO pour les lentilles asphériques
Les dessins des lentilles sont le principal outil pour communiquer les exigences de fabrication et d'essai. Ils sont utilisés à toutes les étapes du processus de création d'optiques par les concepteurs, les vendeurs, les ingénieurs et techniciens de fabrication, les métrologues et l'assurance qualité. Il est essentiel que le dessin soit interprété de manière identique par tous ceux qui utilisent le document, sinon le produit final risque de ne pas répondre aux spécifications prévues.
Heureusement, l'Organisation internationale de normalisation (ISO) a produit une vaste documentation qui clarifie les détails des dessins optiques. La norme ISO 10110 contient un contenu qui détaille la préparation des dessins avec des sections couvrant des sujets tels que les tolérances de forme de surface (ISO 10110-5), les tolérances de centrage (ISO 10110-6) et les dommages induits par laser (ISO 10110-17).
La norme ISO 10110 décrit le format des dessins d'objectifs avec des emplacements standard pour les spécifications d'objectifs couramment utilisées, ce qui permet de trouver facilement les valeurs une fois que la mise en page devient familière.
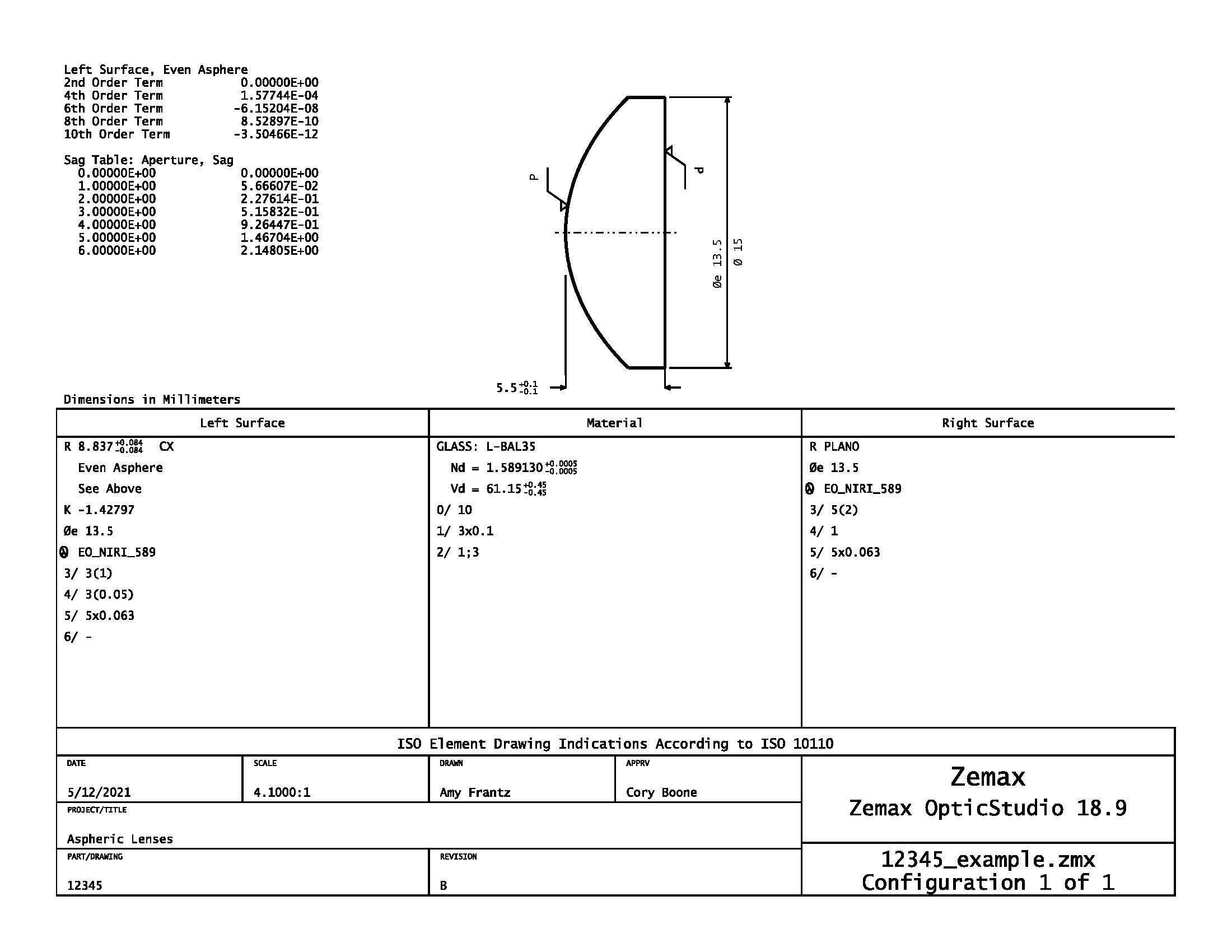
Figure 1 : Ce dessin ISO typique d'une lentille asphérique suit les conventions définies dans la norme ISO 10110. Cliquez ici pour télécharger un PDF de ce dessin pour l'examiner de plus près.
La Figure 1 montre un dessin typique d'une lentille asphérique selon la norme ISO-10110, avec une représentation de la lentille dans la section centrale en haut qui peut inclure des paramètres de base tels que le diamètre et l'épaisseur centrale. Les informations sur le matériau sont contenues dans la région centrale, et les paramètres des surfaces gauches et droites sont contenus dans les cases centrales gauche et droite, respectivement. La section inférieure est laissée pour les détails tels que le titre, la date et l'itération de la révision.
Cette norme de dessin est précieuse pour normaliser les dessins de lentilles sphériques, mais elle est également idéale pour communiquer certains paramètres qui sont essentiels aux performances des lentilles asphériques. La norme ISO 10110-12 spécifie comment décrire les surfaces asphériques sur les impressions, tandis que d'autres sections précisent comment définir les paramètres critiques tels que la rugosité de surface, le centrage, l'erreur de pente et la qualité de surface. L'avantage de l'ISO est que toutes ces valeurs sont clairement définies dans la documentation, de sorte qu'il peut y avoir un consensus entre le client et la fabrication sans qu'il soit nécessaire d'entamer une longue discussion.
Rugosité de surface
La rugosité de la surface peut affecter la diffusion de la lumière et le seuil de dommage laser. Elle est particulièrement importante pour les lentilles asphériques qui sont utilisées pour focaliser ou collimater des lasers de forte puissance. Souvent, les impressions tentent de la préciser avec une indication telle que « rugosité de surface : 10Å ». Il s'agit toutefois d'une spécification incomplète qui peut entraîner des désaccords entre les fabricants et les clients. Il est essentiel de définir le calcul de la rugosité de surface. Une façon courante de définir le mode de calcul de la rugosité consiste à prendre la moyenne quadratique (RMS) de toutes les données. Une autre façon de définir la rugosité consiste à utiliser la valeur moyenne de toutes les données disponibles. La rugosité de surface RMS sera plus élevée que la rugosité de surface moyenne pour le même ensemble de données car elle implique l'élévation au carré de chaque point de données et pondère davantage les valeurs élevées. La norme ISO 10110-8 utilise Ra pour désigner la rugosité moyenne, Rq pour la rugosité RMS pour une longueur d'échantillon, et Sa et Sq pour la rugosité moyenne et RMS pour une zone d'échantillon, respectivement. Une autre préoccupation concerne la bande de fréquence spatiale des erreurs qui est prise en compte. Les erreurs de forme importantes ne sont pas pertinentes pour le paramètre de la rugosité de surface. Il faut donc définir une fréquence de coupure minimale pour exclure les erreurs de forme non pertinentes. À des fréquences très élevées, les données s'approcheront du plancher de bruit de la métrologie, de sorte qu'une valeur de coupure haute fréquence doit également être définie. Les dessins ISO utilisent un symbole de coche pour désigner la finition de surface, avec un « G » pour une surface rectifiée ou un « P » pour une surface polie. La finition de surface pour une spécification de polissage simple peut être indiquée par « P1 », « P2 », « P3 » ou « P4 », P4 indiquant la surface la plus lisse, comme indiqué dans la norme ISO 10110-8. Si une tolérance plus spécifique est nécessaire, la méthode particulière de calcul de la rugosité de surface sera indiquée à droite du symbole de la coche. Entre la méthode de calcul et la coche, la rugosité maximale pour une surface polie est indiquée en unités de nanomètres, et sous la coche, la bande de fréquence est indiquée (Figure 2). Si aucune bande de fréquence n'est spécifiée pour la rugosité, on suppose généralement une plage de 0,0025 mm à 0,08 mm.
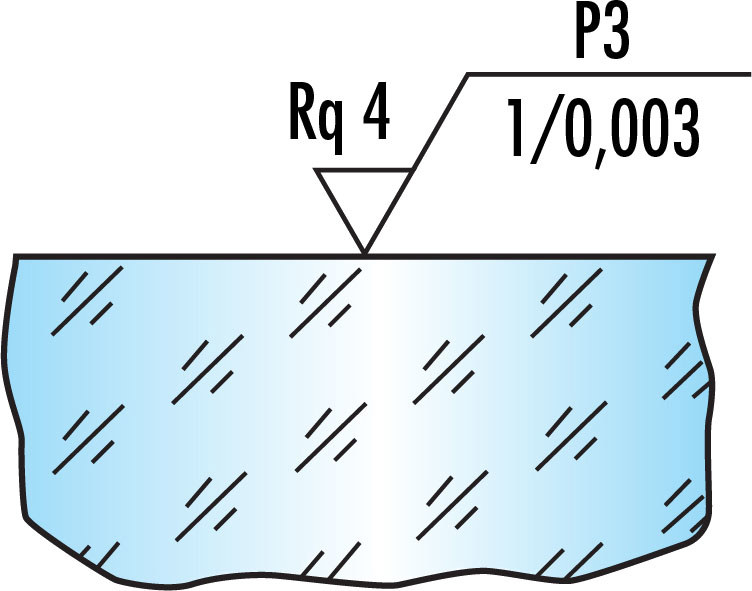
Figure 2 : Cette mention de rugosité de surface ISO indique une surface présentant <16 microdéfauts par balayage de 10 mm (comme indiqué par « P3 ») et une rugosité de surface RMS (Rq) < 4 nm sur une largeur de bande spatiale de 1 - 0,003 mm.
Centrage :
La tolérance de centrage est décrite dans la norme ISO 10110-6. Pour une lentille sphérique, la tolérance sur une surface individuelle est spécifiée par un angle d'inclinaison maximal (σ) par rapport à un axe de référence, qui fait généralement référence au diamètre mécanique extérieur de la lentille. Les lentilles asphériques qui présentent une petite quantité de départs asphériques peuvent également être spécifiés de cette manière. Cependant, une lentille asphérique a un axe de symétrie plutôt que le point de symétrie d'une surface sphérique, il est donc incomplet de ne spécifier qu'une inclinaison. ISO inclut également le déplacement latéral L pour caractériser pleinement le centrage d'une surface asphérique. Le déplacement latéral de la lentille asphérique est la distance entre le point de symétrie de rotation de la surface asphérique et l'axe de référence qui, comme indiqué ci-dessus, est généralement défini par le diamètre mécanique extérieur. La spécification de centrage est écrite comme « 4/σ(L) ». La caractérisation complète du centrage d'une lentille asphérique permet au concepteur de prévoir avec plus de précision les performances de lentille telle qu'elle est construite, plutôt que d'utiliser la valeur unique d'une déviation de faisceau ou d'un faux-rond de surface.
Forme de surface
Les tolérances de forme des surfaces peuvent généralement être exprimées de la même manière pour les surfaces sphériques et asphériques. La forme générale de la spécification dans l'ISO est « A(B/C) RMSx < D ; λ = E ». « A » représente la puissance maximale, ou écart de sagitta, en termes de franges. Elle peut être omise par un tiret si une tolérance de rayon est utilisée ailleurs sur le dessin à la place d'une tolérance de puissance ou être égale à 0 si aucun écart de puissance n'est autorisé. « B » est l'irrégularité maximale des franges, qui peut également être omise par un tiret, et « C » est l'irrégularité invariable par rotation, qui est le plus souvent omise complètement en n'incluant simplement pas la partie « /C » de la spécification. Il est également possible d'omettre complètement « A(B/C) ». Si une tolérance sur l'écart de surface RMS est souhaitée, « RMSx < D » peut être inclus dans la spécification, le « x » indiquant le type de calcul RMS utilisé, où « x » est soit « t » pour la valeur efficace totale de l'écart de la surface par rapport à la forme nominale, « I » pour la valeur efficace de l'irrégularité de la surface, soit « a » pour la valeur efficace de l'irrégularité asymétrique. « D » est la valeur limite pour le RMS. Si l'on souhaite une frange basée sur une longueur d'onde d'une valeur autre que 546,07 nm, il faut inclure « λ = E » où « E » est la longueur d'onde. On trouvera des définitions plus détaillées de tous ces paramètres dans les normes ISO 10110-5 et ISO 14999-4. Si l'on souhaite un autre type de tolérance pour la forme de la surface, par exemple une erreur totale de pic en creux, on peut l'indiquer dans une note sur le dessin.
Erreur de pente
Les lentilles asphériques polies sont soumises à des processus de fabrication de sous-ouverture qui peuvent entraîner des erreurs de forme de surface d'une fréquence plus élevée que les erreurs généralement rencontrées sur les lentilles sphériques fabriquées de manière conventionnelle. Ces erreurs mi-spatiales, comme on les appelle souvent, peuvent avoir des effets néfastes importants sur un système optique et doivent parfois être contrôlées avec une tolérance d'erreur de pente. L'erreur de pente est une mesure de la différence de pente entre une surface souhaitée et la surface réelle sur une longueur ou une zone spécifiée. De nombreuses clarifications importantes doivent être apportées lors de la spécification de ce paramètre afin de garantir une interprétation correcte. Ces précisions portent notamment sur la méthode d’éliminer la tendance des données des mesure brutes, la dimension de la tolérance (longueur ou superficie), l'intervalle d'échantillonnage spatial, la longueur de l'échantillon sur lequel la pente est évaluée (ce qui détermine la fréquence d'intérêt), et le fait que la tolérance soit une valeur de pic en creux ou RMS. Tous ces éléments sont clairement définis dans la documentation ISO et peuvent être mentionnés directement sous les tolérances de forme de surface sur le dessin.
Qualité de surface
Pour ceux qui ont l'habitude de spécifier la qualité de surface à l'aide de la norme militaire américaine MIL-PRF-13830B, le passage aux spécifications ISO peut constituer un changement radical. MIL-PRF utilise deux nombres dans un système Scratch-Dig (rayures - creux), où un nombre tel que « 60-40 » est appelé avec 60 représentant la spécification scratch et 40 représentant la spécification dig. Dans ce cas, le 40 correspond à un diamètre physique maximal de 400 µm dans la taille d'une fouille, mais le 60 doit être comparé à une rayure standard de référence. Une optique doit être inspectée en utilisant des configurations d'éclairage et d'observation spécifiques, et c'est la « luminosité apparente » de la rayure sur l'optique qui est comparée à une norme. Ce test est subjectif, et la taille physique de la rayure n'est pas contrôlée. Contrairement à la norme MIL-PRF-13830B, la norme ISO 10110-7 indique la surface maximale des défauts sans faire de distinction entre les rayures et les crevasses. Elle est donc souvent considérée comme plus objective et reproductible, mais aussi plus difficile et plus longue à inspecter et à calculer. Dans un dessin ISO, la qualité de la surface est généralement spécifiée par 5/N x A, où « N » est le nombre d'imperfections autorisées et « A » est la racine carrée de la taille maximale de la zone d'imperfection en unités de millimètres. La norme ISO permet de séparer les rayures longues et les imperfections du traitement, mais cela n’est pas nécessaire. La norme ISO a l'avantage d'être plus objective, mais la norme MIL-PRF présente un avantage en termes de coûts en permettant une inspection plus rationnelle. Heureusement, les dessins ISO permettent désormais de spécifier la qualité de la surface à l'aide du scratch-dig, de sorte que le concepteur est libre de choisir la méthode la plus logique pour l'application donnée !
Conclusion
Avec un choix de normes multiples, il peut être difficile de sélectionner une norme de dessin, le cas échéant, à utiliser. Les lentilles asphériques, en particulier, ont de nombreux paramètres qui sont importants pour la fonction des lentilles mais qui sont ouverts à l'interprétation selon la façon dont ils sont spécifiées. L'ISO fournit une norme pour les dessins de lentilles asphériques qui définit clairement les aspects importants d'une lentille tels que la rugosité, le centrage et l'erreur de pente, et permet une certaine flexibilité pour d'autres paramètres tels que la qualité de la surface.
Les lentilles asphériques d’Edmund Optics®
Vous recherchez des lentilles asphériques pour votre application ? Edmund Optics® propose plus de 700 modèles d'asphères standard disponibles pour une expédition immédiate, et des lentilles asphériques personnalisées peuvent être fabriquées pour vos besoins spécifiques. Que vous ayez besoin de prototypes ou de gros volumes, les ingénieurs d'Edmund Optics® peuvent créer une solution pour vous.
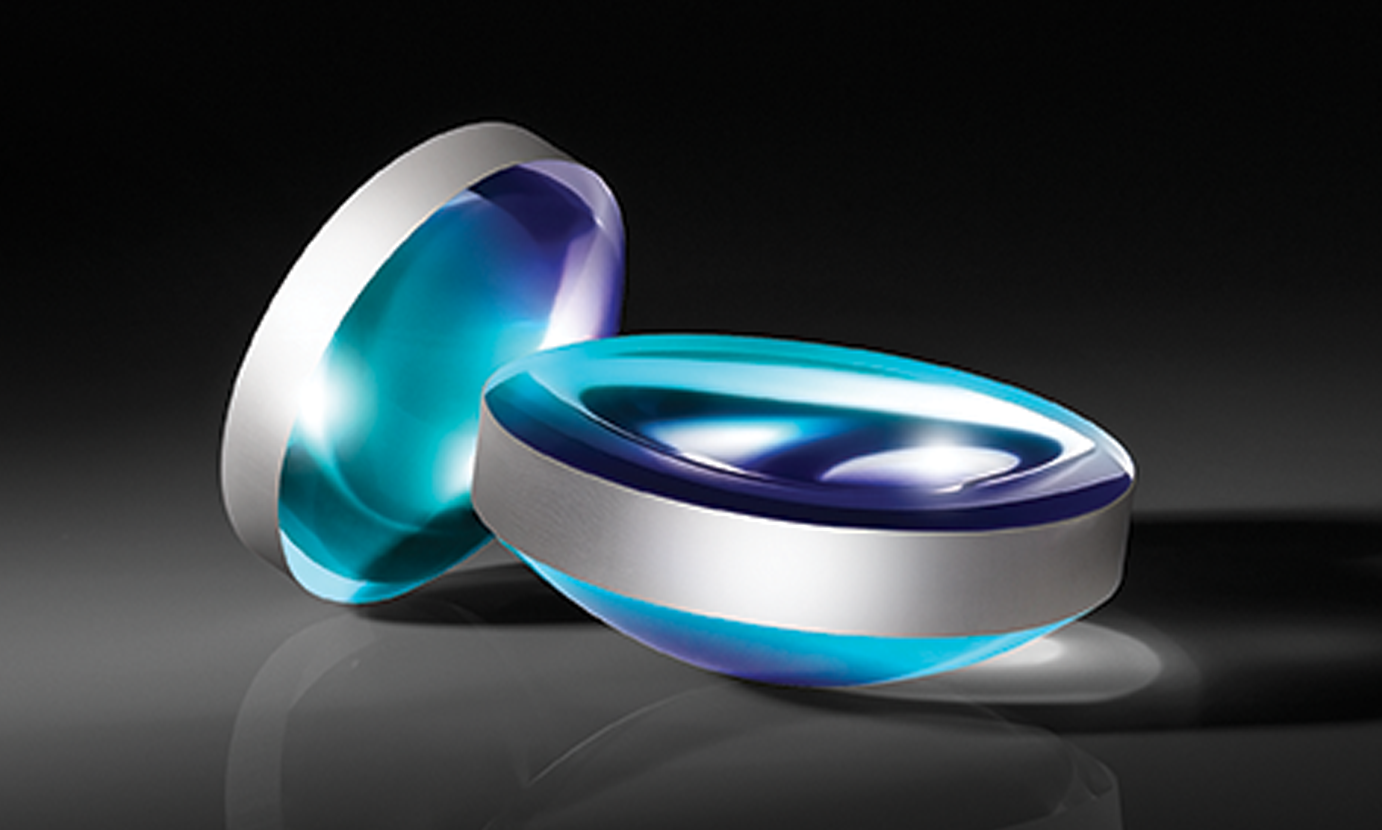
Lentilles Asphériques Polies CNC
Pour les applications exigeant les performances de précision les plus élevées
ACHETEZ DÈS MAINTENANT
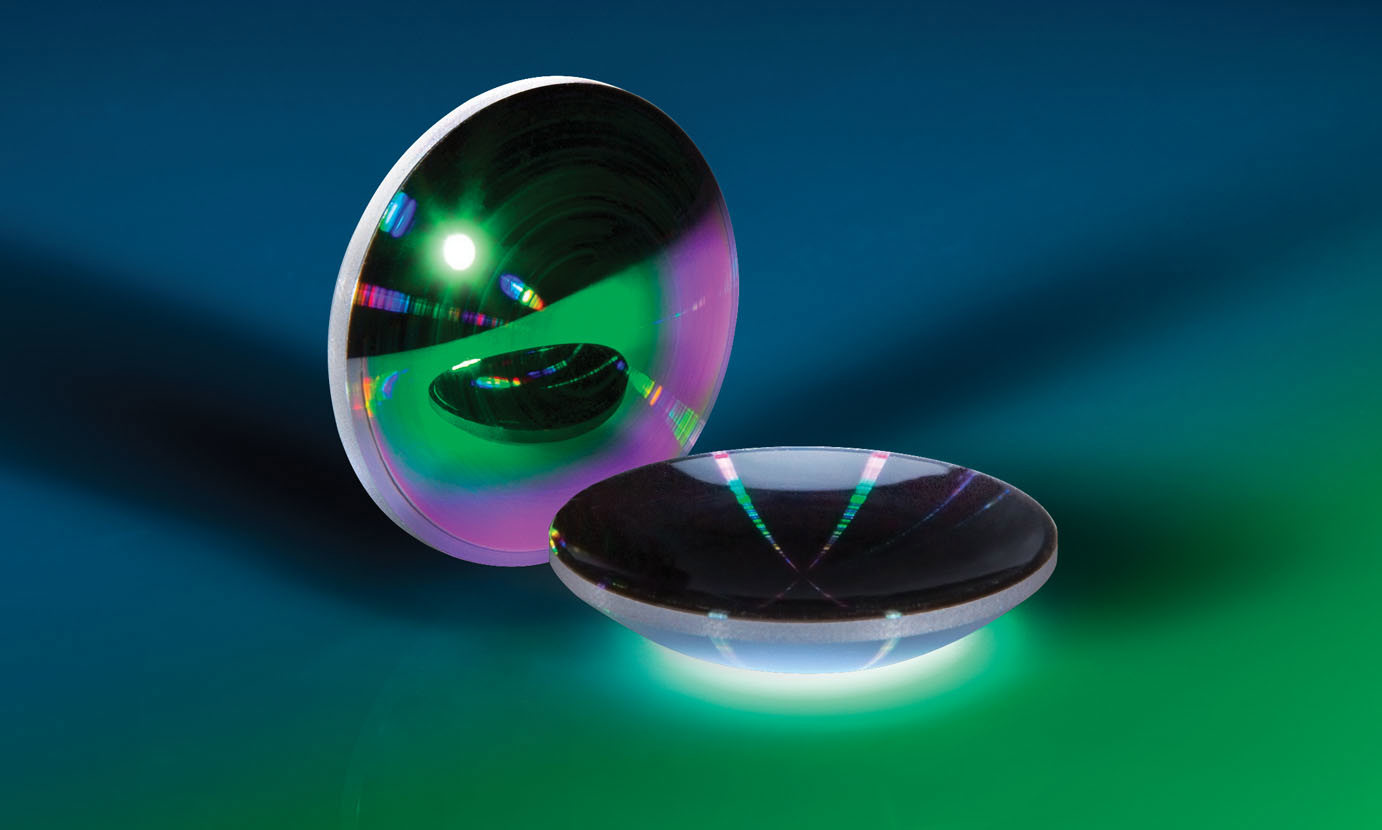
Lentilles Asphériques pour l’IR
Performance limitée par la diffraction dans l’infrarouge
ACHETEZ DÈS MAINTENANT
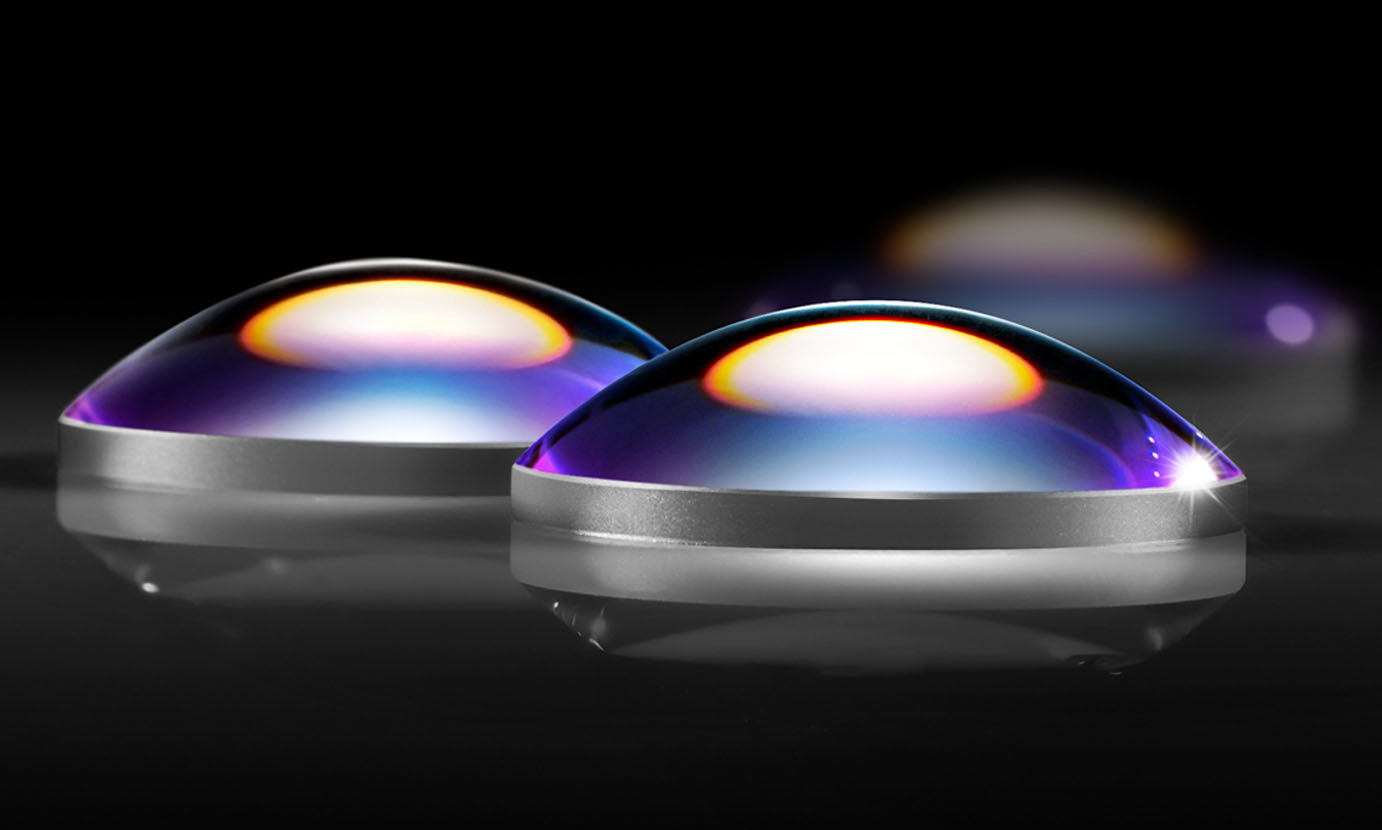
Lentilles Asphériques Moulés en Verre de Précision
Lentilles de petit diamètre pour la collimation et la focalisation laser
ACHETEZ DÈS MAINTENANT
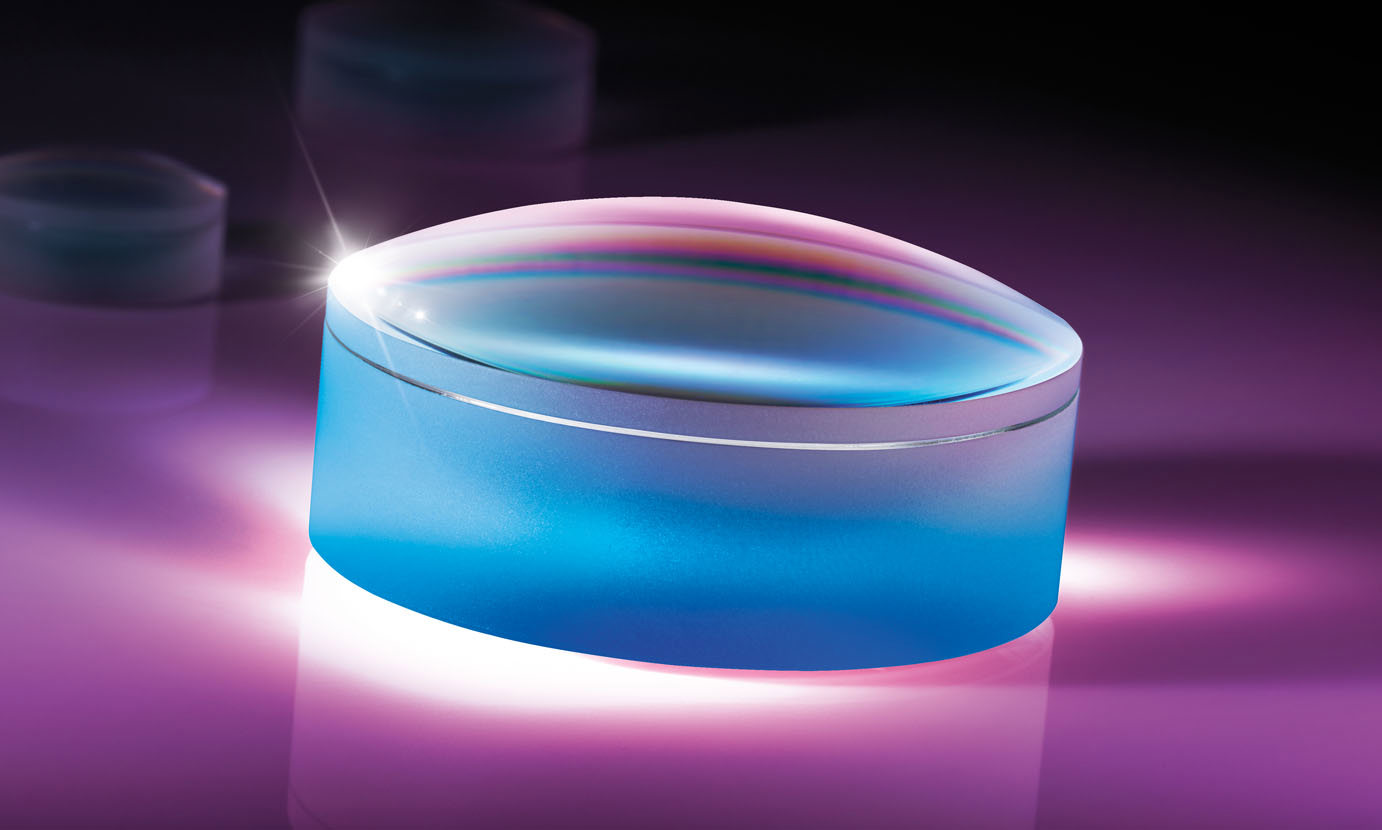
Lentilles Asphériques à Correction de Couleur
Performances sur une large gamme de longueurs d'onde
ACHETEZ DÈS MAINTENANT
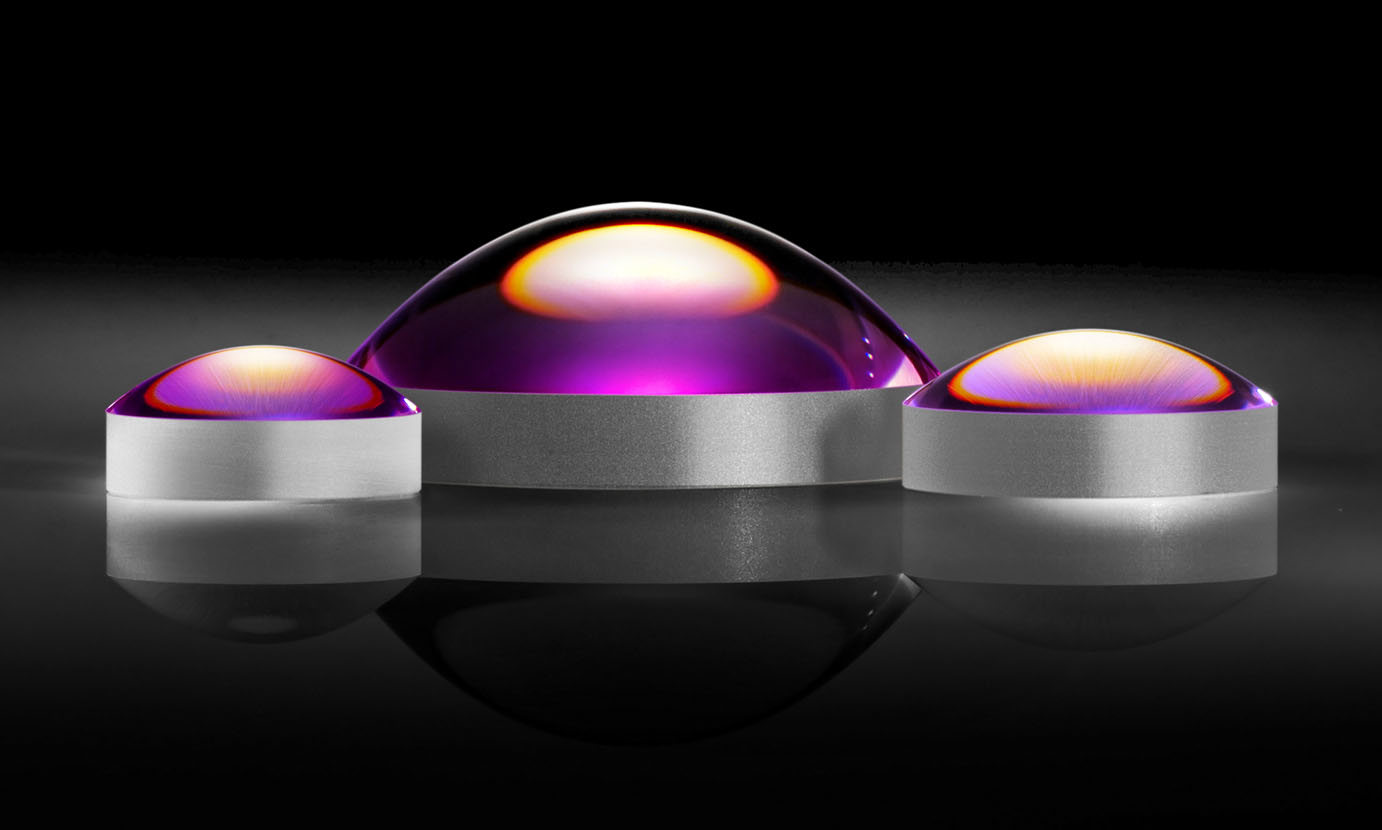
Plus de ressources
- Vidéo : Comment fabrique-t-on une lentille asphérique ?
- Tout savoir sur les lentilles asphériques
- Webinaire enregistré : Conception d’asphères de pointe pour une réalisabilité optimale
- Irrégularité de la lentille asphérique et rapport de Strehl
- Lentilles achromatiques asphérisées
- Vidéo : Sites de fabrication globaux d’EO
- Vidéo : Metrology at Edmund Optics: Vidéo : Measuring as a Key Component of Manufacturing
ou consulter les numéros d’autres pays
facile à utiliser
entrer les numéros de stock pour commencer
Copyright 2023 | Edmund Optics, Ltd Unit 1, Opus Avenue, Nether Poppleton, York, YO26 6BL, UK
L'entreprise Edmund Optics GmbH en Allemagne agit comme un mandataire d'Edmund Optics Ltd au Royaume-Uni. Le titulaire du contrat est Edmund Optics Ltd au Royaume-Uni.