Dommages sous la surface
Cette présentation correspond à la section 8.7 du Guide des Ressources en Optique Laser.
Chaque optique, quelle que soit la minutie de sa fabrication, présente un certain niveau de dommages sous sa surface supérieure, comme des fissures, des contraintes résiduelles, des contaminants et des vides.1 Ces défauts peuvent être causés par le processus de fabrication ou être inhérents au type ou à la qualité du matériau utilisé. Lorsqu’ils sont éclairés par un laser, les dommages sous la surface peuvent augmenter l’absorption et la diffusion, générant de la chaleur et entraînant une diminution du rendement. Ces irrégularités de performance peuvent entraîner une défaillance du système lors de l’utilisation de lasers de haute puissance ou lorsqu’un système est soumis à une contrainte mécanique importante.
Le processus de meulage et de polissage laisse des dommages sous la surface allant d’environ 0,1 µm à des dizaines de microns sous la couche de redéposition du polissage, aussi appelée couche de Beilby. La couche de redéposition est une couche superficielle de l’optique qui est refondue sur de fines rayures de surface dues à une réaction chimique pendant le polissage.2 La couche de défauts sous la couche de redéposition contient la majorité des fissures et autres défauts sous la surface et s’étend généralement de 1 à 100 µm sous la surface de l’optique. Une couche déformée sépare ensuite cette couche défectueuse du matériau en volume sans défaut (Figure 1).
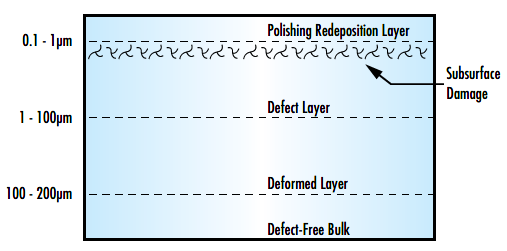
Figure 1 : Dommages sous la surface laissés par les processus de fabrication3
Des impuretés peuvent être piégées dans la couche de redéposition pendant le polissage, à moins que des processus de polissage et de nettoyage spéciaux de qualité prévue pour des applications laser ne soient utilisés. Le polissage avec des grains de plus en plus fins peut réduire encore plus les dommages subis par la surface, mais ces dommages ne peuvent pas être complètement éliminés. Le polissage avec des grains plus fins améliore la qualité de l’optique, mais augmente le temps nécessaire au polissage, ce qui augmente de facto le coût. Un processus de polissage efficace pour les optiques laser garantit l’élimination des dommages profonds sous la surface, tandis qu’un processus inefficace cache simplement les dommages sous la couche de Beilby.
Références
- Fine, Kevin R, et al. “OPTICS FABRICATION: Subsurface Damage Is Measured Nondestructively.” Laser Focus World, June 2006.
- Finch, G. Ingle. “The Beilby Layer on Non-Metals.” Nature, vol. 138, no. 3502, 1936, pp. 1010–1010., doi:10.1038/1381010a0.
- Collier, David, and Rod Schuster. “Superpolishing Deep-UV Optics.” Photonics Spectra, February 2005.
ou consulter les numéros d’autres pays
facile à utiliser
entrer les numéros de stock pour commencer
Copyright 2023 | Edmund Optics SARL, 76-78 rue d’Alsace, 69100 Villeurbanne, France
L'entreprise Edmund Optics GmbH en Allemagne agit comme un mandataire d'Edmund Optics Ltd au Royaume-Uni. Le titulaire du contrat est Edmund Optics Ltd au Royaume-Uni.